Two sites added to Rolls-Royce SMR's UK factory shortlist
.jpg)
In July the company announced six potential locations for the factory, saying the shortlist was selected against a clear set of criteria, picked from more than 100 submissions from local enterprise partnerships and development agencies. They were: Sunderland in Tyne and Wear, Richmond in North Yorkshire, Deeside in Wales, Ferrybridge in Yorkshire, Stallingborough in Lincolnshire and Carlisle in Cumbria.
Two more locations - Shotton, Deeside, in North Wales and Teesworks, Redcar, in north east England - have now been added after the sites met the shortlist criteria for the first of three expected factories in the UK, which will produce the vessels for the 470 MWe pressurised water reactor.
Rolls-Royce SMR's chief operating officer David White is to oversee the construction of the factories which will be needed to construct the planned fleet of SMRs, each capable of generating the same amount of electricity as about 150 onshore wind turbines, and enough to power a million homes.
All the potential sites are to be visited over the next six weeks ahead of the next stage of the site-selection process.
White said: "The overwhelmingly positive response, resulting in more potential sites than we might have hoped for, means we have more information to assess but is vitally important in helping us select the right locations for our factory."
The Rolls-Royce SMR design was accepted for Generic Design Assessment review in March with the UK's Department for Business, Energy and Industrial Strategy asking the Office for Nuclear Regulation along with the environment regulators for England and Wales to begin the process.
To minimise the construction phase of the programme, the Rolls-Royce SMR is fully modularised with the reactor, about 16 metres by 4 metres, able to be transported by road, rail or sea. Targeting a 500-day modular build, the firm says this concept minimises the onsite time and effort required to construct and build the plant, with about 90% of manufacturing and assembly activities carried out in factory conditions.
_59102.jpg)
_49833.jpg)
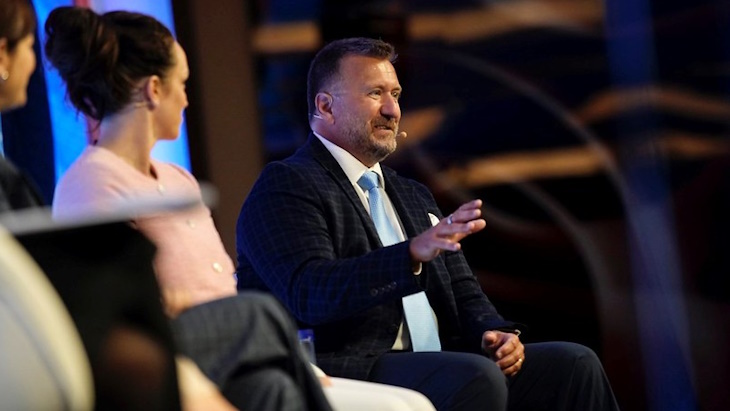
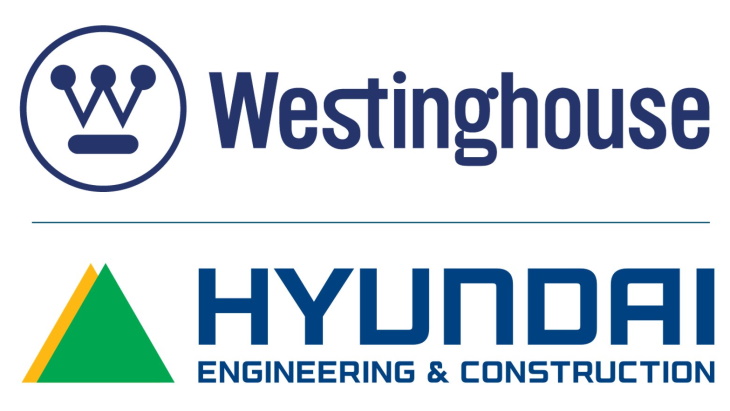
