Viewpoint: Nuclear in the fourth industrial revolution
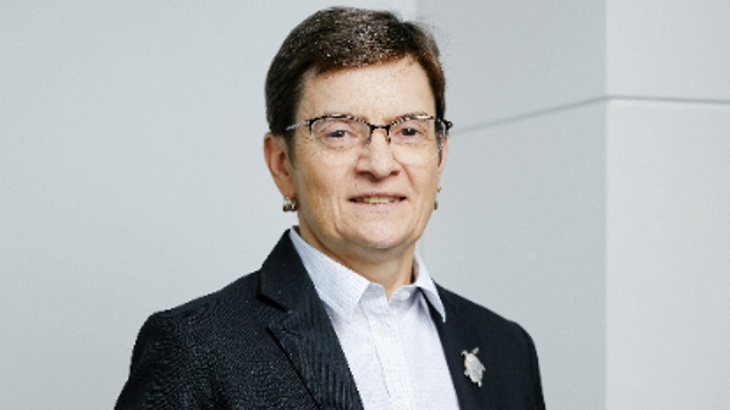
"For centuries, industrial revolutions have shaped the world and propelled society forward with technological advancements and innovations. In the 18th Century, the first industrial revolution introduced new possibilities with mechanisation and the introduction of technologies like steam engines, which revolutionised the economy by speeding up transportation and expanding industry and manufacturing.
The second industrial revolution harnessed new energy sources such as oil and gas, and electricity became available in homes and businesses, changing the way people lived and worked. In the mid-20th Century, the third industrial revolution saw the invention of the personal computer and the internet, linking economies and people through an enhanced global marketplace marked by high levels of automation.
Today, the fourth industrial revolution, which blends human behaviour with technology, continues to transform the way people live, work and interact with one another. For example, the Internet of Things allows smart devices to connect to the home, managing everything from lights to thermostats, to safety and security systems. Companies use artificial intelligence to monitor and control their inventory in warehouses, reducing costs and increasing efficiency. Virtual and augmented reality enhance training in fields ranging from medicine and health care to electricity generation.
As a reliable and carbon-free source of electricity that is available 24 hours a day, seven days a week, nuclear energy has an important role in powering the fourth industrial revolution. It’s also an industry where experts and innovators are constantly evaluating and incorporating the latest breakthrough technologies, including those from the latest industrial revolution, to ensure the continued efficient production of electricity.
The nuclear energy industry is embracing the latest technologies to enhance the way that workers operate and complete maintenance activities to support today’s fleet of reactors. For example, virtual reality creates immersive experiences that allow personnel to train, prepare for and even practise activities before they arrive at a plant site. Workers can decide how they will need to organise and position equipment to complete work in the safest and most efficient way. Once they are on-site, augmented reality applications feed important data, such as radiological activity and dosimetry, to field workers.
Augmented reality technologies became even more crucial during the COVID-19 pandemic when restrictions cancelled travel and reduced on-site activities at nuclear power plants. These technologies allow companies to connect experts in different and sometimes remote locations to solve problems, mobilise resources and share feedback on designs and engineering in real-time with direct input from workers in the field.
For example, a nuclear power plant in France required support during its spring 2020 outage to maintain fuel cleaning operations on schedule and ensure continued, reliable electricity generation. Augmented reality technologies allowed on-site workers and Framatome experts from around the world to connect remotely to share information and complete the necessary maintenance.
New applications of artificial intelligence also support asset management in the nuclear sector. So-called edge computing allows operators and other personnel to retrieve rich analytics and provide qualified warnings to drive actions to prevent lost performance while improving maintenance plans.
For instance, algorithms can classify patterns from acquired signals and time series data. That allows experts to connect patterns to failure modes and deliver valuable insights about assets’ condition. This information provides plant operators with actionable insights to quickly make smart, informed decisions to optimise asset management and operational expenditures. By automatically collecting relevant asset data and centralising that information in one single storage and processing platform, asset owners also avoid recurrent costs associated with inspection routines.
For example, a nuclear power plant in Europe worked with Framatome to deploy a data analytics and predictive maintenance platform. The plant used this platform, the central asset data intelligence system (CADIS), on its secondary circuit to monitor more than five components and evaluate higher stresses due to planned load follow operations. Monitoring the moisture separator and preheater, the feedwater preheater and the condensate piping system provided engineers with precise information about stresses and wear that may occur to these components during such operations.
At a plant in Asia, abnormal vibration amplitude was observed during the commissioning phase of a reactor coolant pump. Personnel considered a full-stop in the project to inspect the system but were able to localise the problem using CADIS analytics. The root cause was completed within two weeks. Avoiding the full-stop during commissioning saved the plant about 10 to 15 days minimum in its project schedule, resulting in direct cost savings.
Another application of fourth industrial revolution technologies can be found in a broader effort under way to pool research and development related to nuclear reactor digital twins. EDF Group, Framatome, the French Alternative Energies and Atomic Energy Commission and six additional organisations from academia and the French nuclear industry, are bringing together more than 100 experts to digitally clone every reactor in the French nuclear fleet. The cloned reactors will serve as a training simulator for the new generation of operators and a simulation environment for engineering studies.
Digital twins also provide a bridge between the digital representation, or model, and physical plant data. By connecting digital twins with their associated fault libraries, abnormal behaviour in a plant system can be detected so that any problems can be identified and addressed early. This technology will also be critical as reactor developers design the next generation of technologies, with the goal of reducing operation and maintenance costs so they are closer to that of a combined cycle natural gas plant, which are around seven times lower than a legacy nuclear power plant.
Generations of industrial revolutions have brought about significant technological changes and advancements. As the fourth industrial revolution continues to unfold, innovators will find new ways to blend human behavior and technology that will continue to change the way people live, work and interact with one another. People will continue to find new ways to collaborate and work together, bridging vast distances. Connected devices will inform daily life like never before. The possibilities are endless."
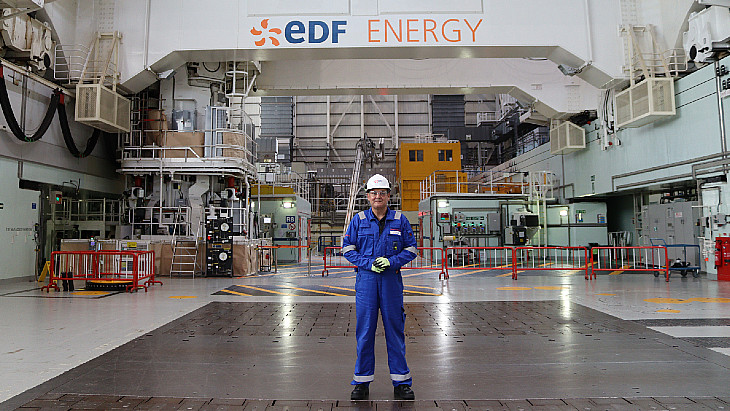
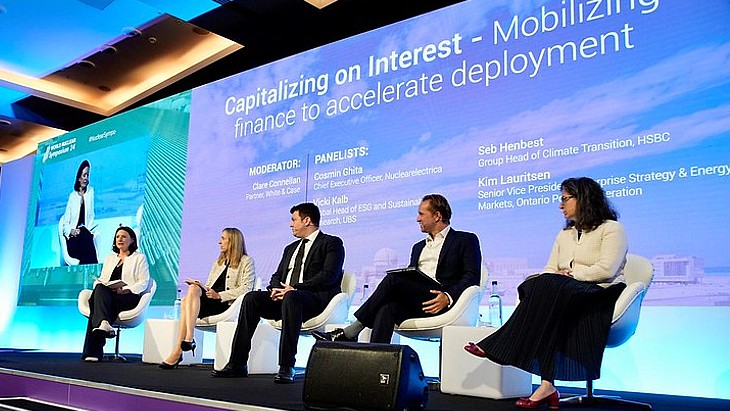
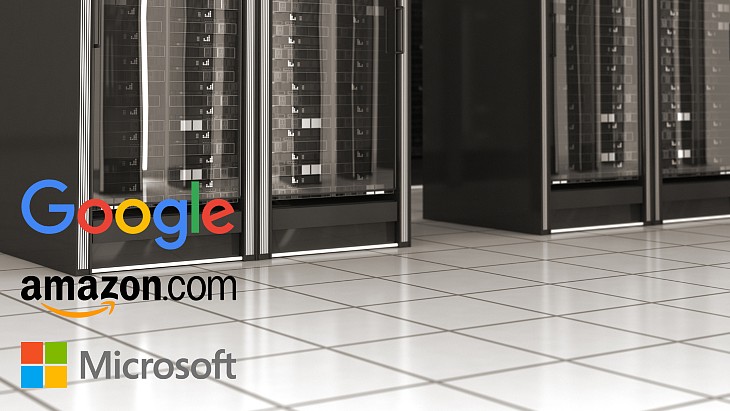
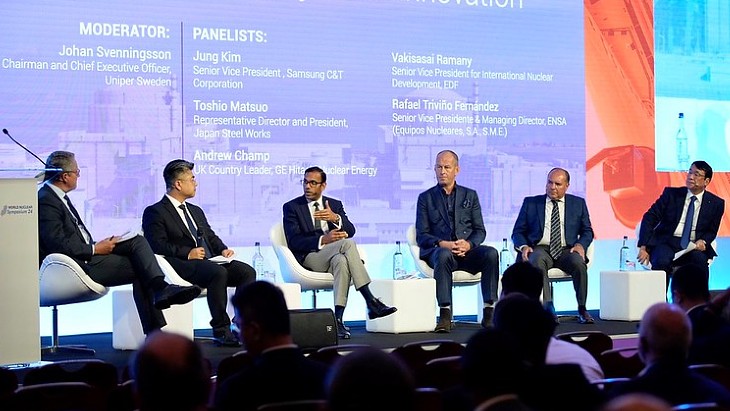
