Innovation is key to industry's resilience, says Westinghouse
.jpg)
Speaking at the World Nuclear Association Symposium 2018 in London, Westinghouse President and CEO José Gutiérrez described the company’s strategy following its recent exit from bankruptcy protection, while Michele DeWitt, the company’s senior vice president for nuclear fuel, described some of the innovative technologies it is working on.
Westinghouse Electric Company LLC was formed in 1998 from the nuclear power division of the original Westinghouse Electric Corporation that was founded in 1886. In 1957, it supplied the world’s first pressurised water reactor - the Shippingport Atomic Power Station in Pennsylvania, which was in operation until 1982. Today, Westinghouse technology is used in more than half of the 450 reactors in operation around the world and 131 of them run on its fuel. In July, the world's first AP1000, a Westinghouse reactor design, achieved grid connection and power generation at unit 1 of the Sanmen nuclear power plant in China.
Westinghouse filed for Chapter 11 bankruptcy protection with US courts in March 2017 to enable it to undergo strategic restructuring. The filing affected only its US operations, which included projects to construct four AP1000 reactors at two sites, Vogtle in Georgia, and VC Summer in South Carolina. On 4 January, it was announced that Brookfield Business Partners had agreed to acquire 100% of Westinghouse from Japan's Toshiba Corporation for about USD4.6 billion. On 1 August, Westinghouse announced completion of the sale, which marked its emergence from Chapter 11 as a reorganised company.
Gutiérrez told delegates at the symposium today it was “really remarkable” it had emerged from bankruptcy protection within 16 months.
“We’ve streamlined our operations and reduced overhead costs to drive efficiencies and we’ve done that whilst also expanding our base business, which means the company continues to be an industry leader.” He added: “And the best way to support the operating fleet and also to build new ones is through innovation.”
Chinese success
Gutiérrez described the AP1000 at Sanmen 1 as “the world’s first true Gen-III+ nuclear power plant” and referred to praise of the technology from Wang Binghua, chairman of State Nuclear Power Technology Corporation (SNPTC) at the symposium yesterday.
“The news coming from China is that the unit is working as planned, that the most advanced technology in the world is succeeding,” Gutiérrez said, adding that all first-of-a-kind challenges connected with the design have been solved.
Binghua told delegates that a passive safety test had been successfully conducted at Sanmen 1, proving its passive safety capabilities.
“Last week we had five full days of a full power loading operation. Then the reactor was suddenly shut down manually and then all the operating four reactor coolant pump were shut down manually. Then started the heat exchange. We took 12 minutes to transfer the residue heat to the used fuel pool. We were so impressed by this passive safety feature which supported the transfer of residual heat to the used fuel pool. We appreciate very much the outstanding engineering design from Westinghouse.”
Gutiérrez noted that three of the four AP1000s under construction in China - Sanmen units 1 and 2 and Haiyang unit 1 - had been connected to the grid. Connection of Haiyang 2 is expected next week.
Mingguang Zheng, senior vice president of SNPTC, today gave delegates the scheduled dates for Haiyang 2 as 14 September for grid connection and 11 December for the start of commercial operation. Commercial operation for Sanmen 1 and 2 are expected, he said, on 28 September and 8 November, respectively. For Haiyang 1, this is expected on 25 October.
Commitment
Westinghouse continues to learn the lessons of its projects and to innovate for one reason, Gutiérrez said. “We believe that nuclear energy is more valuable to the world energy mix than ever before.”
A study released last week from the Massachusetts Institute of Technology Energy Initiative, states that the challenge of climate change will be harder and costlier to solve unless nuclear energy is included in the energy mix.
Referring to this study, Gutiérrez said: “Examples in the EU and the US show that when a nuclear power plant is shut down it is replaced by coal and gas and not by renewables”, making it impossible to achieve climate goals. The fact that nuclear does not emit greenhouse gases is critically important, he said, for example to quality of life in China and India.
Fuel
Westinghouse designs and manufactures more types of nuclear fuel than any other supplier, DeWitt told delegates at the symposium yesterday, and currently supplies nuclear fuel to one-third of operating reactors, including pressurised water, boiling water and advanced gas-cooled reactors.
She said it is crucial the fuel manufacturing industry “delivers what matters” by providing the lowest fuel cycle costs; operational flexibility; higher burnup capability; supply diversity; accident tolerant products; and robust fuel performance.
“The landscape in which we operate is changing rapidly and our ability to innovate is critical,” she said. The nuclear industry faces competition from renewables and natural gas; utility customers are increasingly facing the need to shift their nuclear assets from baseload to load follow; operating fleet life extensions are under way; and new build reactors are based on new technologies.
“I believe that our industry has a bright future ahead and the ability to innovate will be the key to unlocking that success. We will develop new ways of thinking about challenges, invest in transformational technologies from both inside and outside the industry and continue to develop new products and processes while focusing on providing unparalleled delivery to our customers. We must deliver what matters,” she said.
Headquartered in Cranberry Township, Pennsylvania, Westinghouse is present in 19 countries and understands that risk management and security of supply for economic and national security reasons is a growing priority globally, DeWitt said.
“Our nuclear industry’s future relies on our collective ability to operate both the existing fleet and new build in a manner that leverages the asset investment to a greater degree than ever before. As industry needs evolve, nuclear fuel providers are being called upon to deliver more, without compromising safety or reliability. The lowest fuel cycle cost possible, an increased degree of operational flexibility, higher burnup capability to generate more power for fewer modules, diversity of supply, accident tolerant products to generate resilience and survivability in beyond design basis accidents, all in addition to robust and leak-free fuel performance.”
Westinghouse’s commitment to new technology is “shared and encouraged” by its new owners, Brookfield, and the company is “investing for the future”, she said.
Products
Some of its key innovations include its “game-changing” EnCore fuel, she said.
“Our EnCore family of products provides not only enhanced accident tolerance, but also improved fuel cycle economics. It’s being developed to deliver design basis tolerance safety margins and withstands far more serious conditions than today’s fuel.
“Having fuel that can withstand the most severe accident scenarios is game-changing for utilities. The right fuel can also bring significant plant and operational savings by improving fuel cycle economics and enabling longer fuel cycles.”
Westinghouse expects its coated cladding and advanced pellets could be provided in lead test assemblies by 2021 and in reload quantities from 2023, she said. In addition, silicon carbide test assemblies will be rolled out in 2022 with reload quantities beginning in 2027.
The company expects to deliver a lead test assembly of its TRITON11 boiling water reactor fuel to Finland’s TVO for insertion in Olkiluoto unit 2 in January next year and to unit 3 of Swedish OKG’s Oskarshamn plant in June the same year. It is targeting full reload introduction in Europe and the USA in 2023 and 2024, respectively, she said.
The company is also meeting customer demand for diversification and security of supply with its advanced VVER fuel designs, she said. Westinghouse produces fuel for VVER-1000 reactors at its facility in Västerås Sweden. It is currently providing fuel to six of Ukraine’s 15 power reactors, which will increase to seven at the beginning of 2021.
“Recently we were pleased to join the celebration for the loading of South Ukraine NPP unit 3 for the full core of Westinghouse fuel. This is the first unit in Ukraine to operate with 100% Westinghouse VVER fuel.
“We are also actively working with other customers to expand our VVER-1000 supply and will provide six lead test assemblies featuring our next generation VVER design to Temelín unit 1 in the Czech Republic. And we’ve also led a consortium to develop a conceptual VVER-440 fuel design and determine the establishment of manufacturing and a supply chain to fabricate and transport VVER-440 fuel assemblies,” she said.
Another innovation Westinghouse is exploring is 3D printing, she added. “We can produce components for complex geometric and design margins that would otherwise not be possible. 3D printing has also enabled us to accelerate the development process by shortening the time to develop prototypes and bring these products to market.”
Its BlueRad camera assists with fuel assembly visual inspections “whilst providing state-of-the-art optical quality for underwater inspections,” she said.
Quiver Fuel Rod Storage, another product it has developed, is “a simple and safe system” of handling the storage of failed PWR and BWR fuel rod fragments, DeWitt said, adding that its size allows it to be handled in the same way a PWR or BWR fuel assembly would be.
The company is also focusing on innovation software to enhance safety margins, support flexible operations and improve modelling and fuel performance, she said.
_59102.jpg)
_49833.jpg)
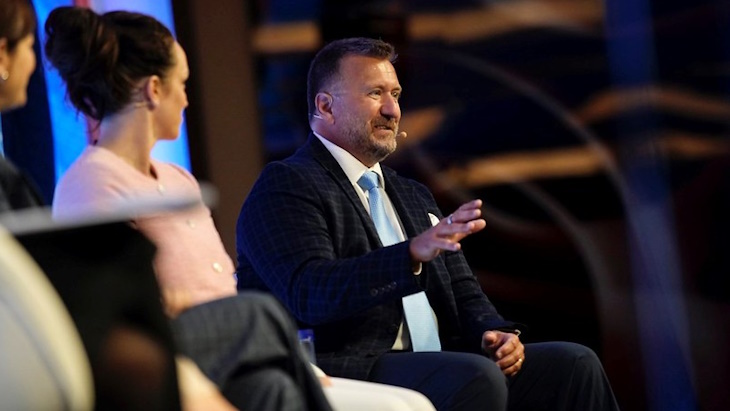
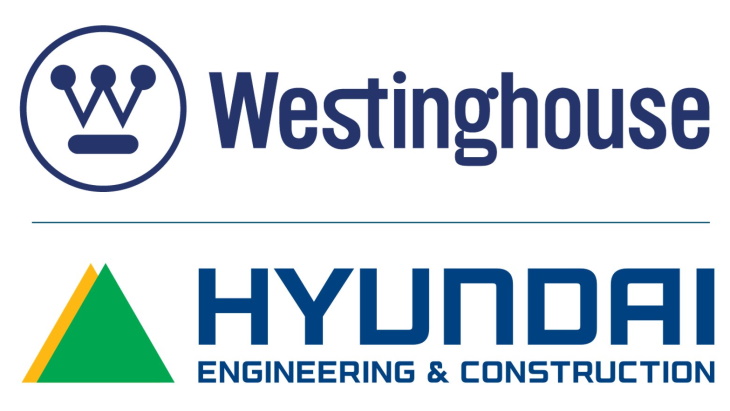
