Breaking new ground in the EPC supply chain
A robust supply chain is needed to enable new reactors to be built on time, on budget and at the scale needed to meet decarbonisation goals - and major players in the nuclear engineering, procurement and construction sector shared some of the experiences and lessons learned from projects both nuclear and non-nuclear at World Nuclear Symposium 2024.
.jpg)
Bechtel took over construction of the Vogtle new-build projects in the USA in 2017. More recently, the company has a contract with Westinghouse to build three AP1000 units in Poland, which, as well as addressing national energy security and climate goals, provides an opportunity to train thousands of professionals and workers in nuclear work and help to establish a supply that can be utilised and replicated in future AP1000 projects, Ahmet Topkinar, general manager of Bechtel’s Nuclear Power business line, said.
Innovation and standardisation are key factors for improving schedule time, values and cost services, he said. Being involved from the very start of a project - which, unlike the Vogtle project, is the case for Bechtel at Terra Power's Natrium construction project at Kemmerer, Wyoming, means that design engineers can check for "constructability", and this minimises the need to rework aspects of the project, which in turn saves time and money.
Tokpinar also spoke of the value of an integrated EPC approach, a lesson learned from Bechtel's non-nuclear projects. "What we do on our non-nuclear projects, which we are implementing now on our nuclear projects, is a totally integrated digital delivery platform," he said. "And what I mean by that is you create a common data environment where all the data resides. You have all your other programmes and tools that connect, read back and forth, whether it's your construction material, tracking tools, your engineering design tools, your procurement system, they are all connected to this single source of data."
As well as minimising the errors from "chasing paper", this approach makes it much easier to visualise and plan construction activities. Doing this advance work packaging before mobilising at the site saves time, he added. The company is aiming for a completely paperless, digital workflow to improve productivity. "We think this is going to be a game changer, a paradigm shift in the nuclear industry," he said.
But there are two challenges that are holding back the development of a repeatable nuclear supply chain, Tokpinar said. "One is funding - and the firm commitments from governments and customers alike to identify the pipeline of projects. There has to be some consolidation from customers around picking winners," he said. "The second is standard design … a point where we have a standard design that is licensable under at least certain jurisdictions, that can be truly replicated, then we will achieve the nth-of-a-kind benefits of using the same supply chain, same design, rolling crews and professionals from one project to another. It's not rocket science."
"I think we do a very good job as an industry advocating for nuclear. But now we need to take responsibility to deliver it with success," Tokpinar said.
Time is money
Stéphane Aubarbier, deputy CEO at Assystem, also felt that a broader use of digital tools could be a game-changer for nuclear projects.
Finance - or more specifically the cost of finance for nuclear projects - is a key consideration, said. This is especially so for newcomer countries to nuclear. "It is not that they don't find money: it is that they find money at too expensive a cost," he said. Improving project timelines will help to decrease the cost of financing, he said. "So if we have a material design phase that is very short, we have less rework during the construction, and then we can hope that the construction phase will be shorter than expected," and not overrun, he said.
But even more important is improving methods of construction, and here digital tools will be a game-changer, he said. Nuclear is a document-based industry, so transitioning from being document-oriented to being data-oriented will require a change in mindset, but will be the main way to shorten nuclear power plant construction times. This will also decrease the risk profile of the industry, and decrease the cost of finance, he said.
"As soon as we do that, we would see the cost of funding decreasing, it would be more affordable and then it will take pave the way for many more countries to step into nuclear programmes," Aubarbier said.
L-R: Bernard Fontana, Stéphane Aubarbier and Esra Songur (Image: World Nuclear Association)
Business model
The four-unit Akkuyu plant, currently under construction, is Turkey's the first nuclear power plant and the first anywhere to be built under a build-own-operate model, with Russian atomic company Rosatom responsible for construction, operation, commissioning and personnel training. Esra Songur, advisor to the deputy CEO of Akkuyu Nuclear JSC, told the panel that this approach offers strong project management through alignment with Rosatom's established management infrastructure.
"The model has significantly impacted the implementation of our project," she said. "This gives to us some challenge because this is the long term responsibility, and a key lesson learned from the project is that communication stakeholder management is crucial," Songur said. "We will be an integral (part) of this community for 60 years or more. The supply chain is another important subject for us: we have 400 companies, customers, of which most of them are local," she said. The local supply chain is crucial for to manage the project efficiently: "So our first priority and and key lessons will be is stakeholder management."
Being ready
Asked what lessons Framatome has learned from recent projects - and what needs to be done to ensure the supply chain is able to support the construction of many new reactors, Framatome CEO Bernard Fontana had a very simple answer. "First, be ready," he said. This means investing in developing the workforce with the skills and expertise necessary for nuclear projects - which Framatome has doing via skills academies. The company has been investing in its industrial capabilities too, to enable it to produce a flow of components such as steam generators, and making acquisitions to assure its supply chain for components such as pumps and turbine technology.
Asked what his key takeaways for the audience would be, Fontana named his three "obsessions" of safety, quality, and lead time. "And this also relies on the engagement of the teams - suppliers, contractors, customers... So let's mobilise our team in the one team spirit."
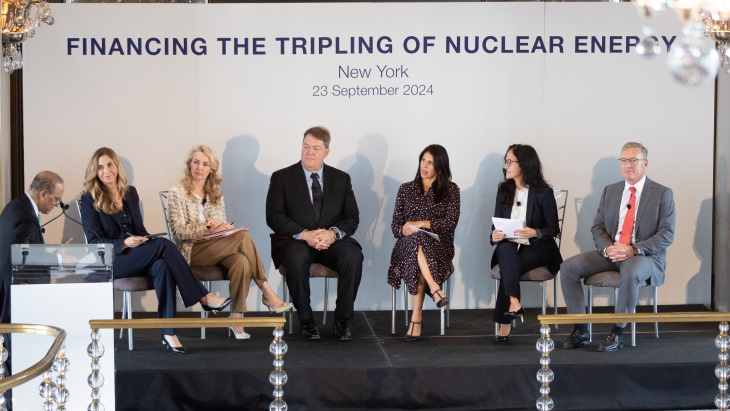
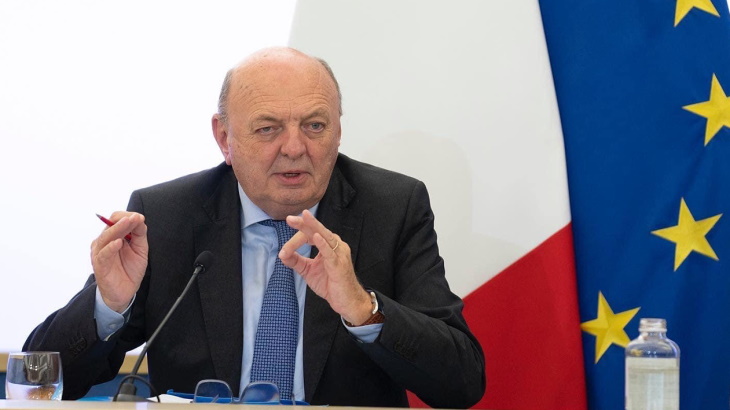
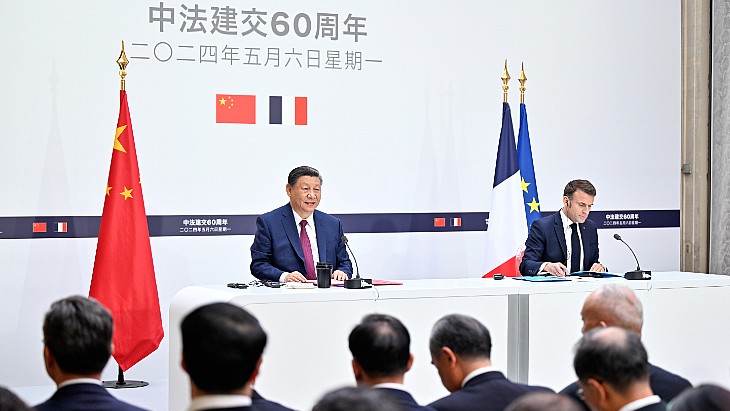
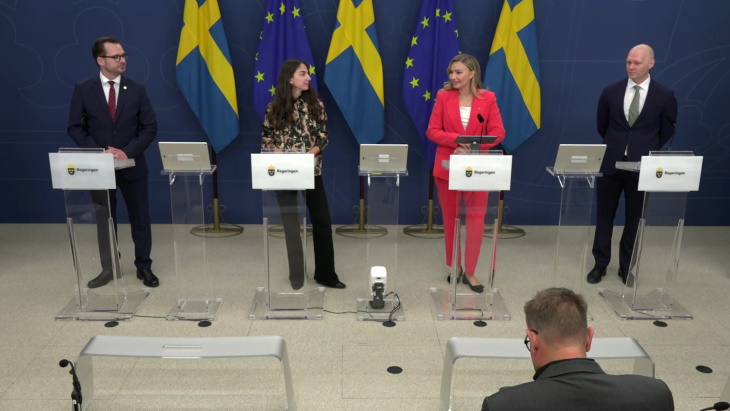
