Framatome and GA team up on fast modular reactor
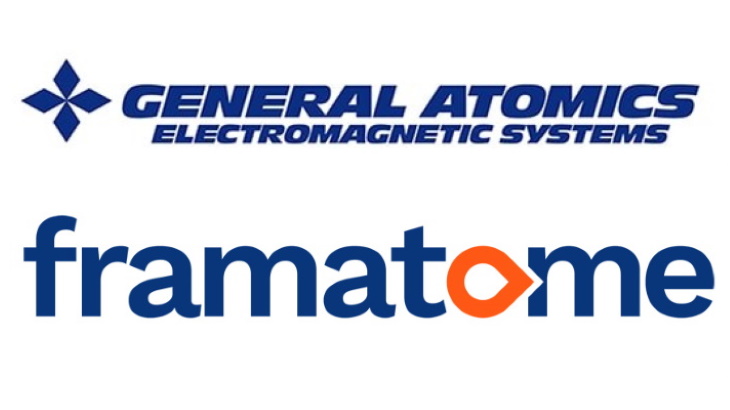
The FMR will be designed for enhanced safety and ease of operation with fast-response load following and overall high efficiency, General Atomics said. The passively safe gas-cooled FMR will use a non-hazardous helium coolant - a chemically-inert gas that is non-explosive, non-corrosive and does not become activated. Because the reactor is dry-cooled and uses virtually no water to operate, it can be sited nearly anywhere, it said. The power conversion forgoes the use of complex steam generators and pressurisers, and the fuel will operate for approximately nine years before requiring replacement.
The direct helium Brayton cycle enables fast grid response, with up to a 20% per minute power ramping rate for load following, and high overall efficiency of 45% during normal operation. The automatic control of the reactor power and turbomachinery keep the reactor at a constant temperature that mitigates thermal cycle fatigue associated with most load-following reactors.
Due to its advanced modular design, the FMR reactor can be built in a factory and assembled on-site, which helps to reduce capital costs and enables incremental capacity additions.
Framatome's US engineering team will be responsible for designing several critical structures, systems and components for the FMR.
"This collaboration builds on our long relationship with General Atomics with a shared interest in advancing nuclear energy technologies to create a cleaner world for generations to come," said Framatome CEO Bernard Fontana. "With our experience and expertise in designing reactor systems and components for advanced and small modular reactors, our team is helping to make that vision a reality."
"Designing and deploying a safe, cost-effective, modular reactor is critical in helping the world move closer towards a clean energy future," said GA-EMS President Scott Forney. "We look forward to leveraging our two companies' decades of experience in advancing nuclear technology and demonstrating the next generation of commercially viable nuclear reactors."
Christina Back, vice president of nuclear technologies and materials at GA-EMS, added: "For a clean energy future, GA-EMS is bringing together the team and technologies to realise a community-friendly, advanced nuclear plant that works seamlessly with renewables." She said there is strong interest across the industry in the future commercialisation of the FMR. "Our design will employ technologies for safe and reliable operation that can be sited virtually anywhere to expand distributed electricity generation."
The GA-EMS led team aims to complete a demonstration of the FMR - which will verify the design, manufacturing, construction and operation of the technology - in the early 2030s. Commercial deployment is anticipated by the mid-2030s.
General Atomics has also been developing its Energy Multiplier Module (EM2) small modular reactor design. This is a modified version of its Gas-Turbine Modular Helium Reactor (GT-MHR) design. The EM2 employs a 500 MWt, 265 MWe helium-cooled fast-neutron high-temperature reactor operating at 850 degrees Celsius. This would be factory manufactured and transported to the plant site by truck. It is designed to operate for 30 years without requiring refuelling.
"The FMR is a new design separate from the EM2," Back told World Nuclear News. "There are commonalities with the use of direct Brayton cycle for higher thermal efficiency as well as the fast neutron spectrum of the reactor core, but those are the only main commonalties.
"Some of the FMR’s key systems and fuel are quite different from EM2 and are specifically designed for the smaller sized FMR and for meeting the demonstration and deployment timeframes. We see the FMR as a nearer-term offering that can meet the power market needs of the mid-2030s," she said. "Having said that, we are still pursuing longer-term demonstration and deployment of the larger base-load EM2 power plant."
_92619.jpg)
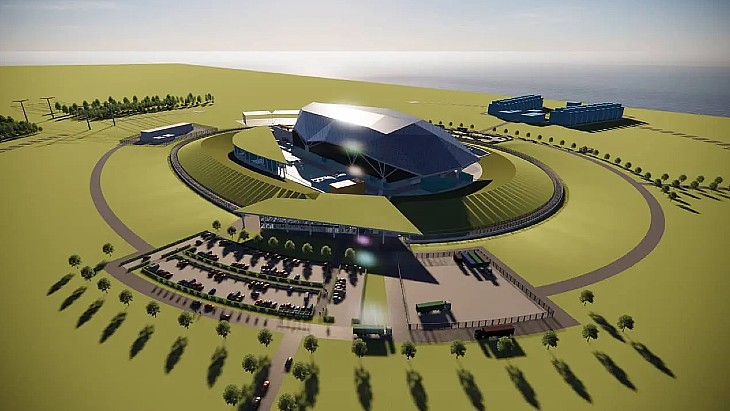
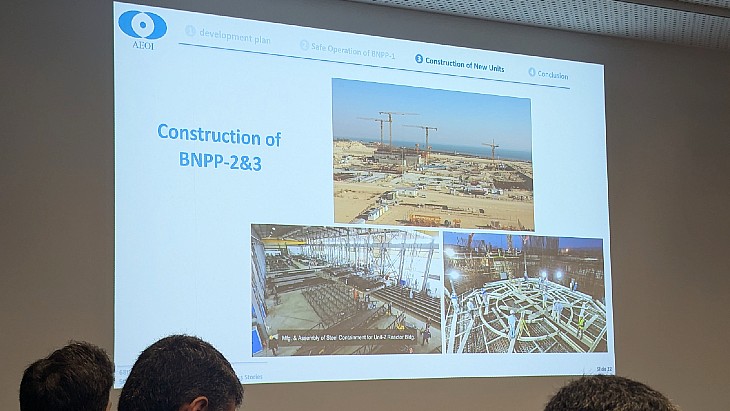
_84504.jpg)
