ITER to replace 23km of cooling pipes on thermal shield panels
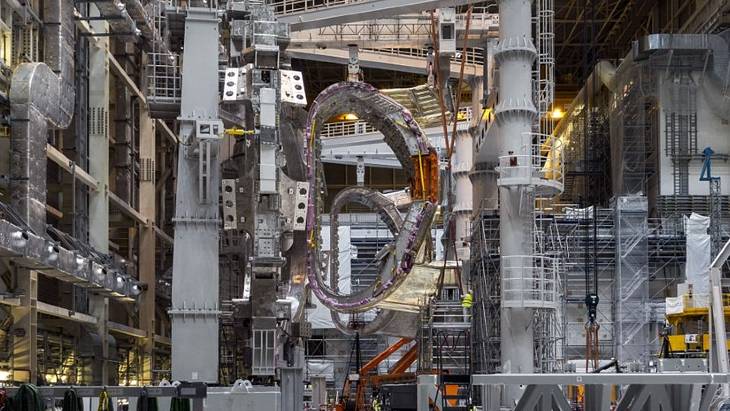
ITER Director General Pietro Barabaschi said that the challenges being faced were common to many first-of-a-kind ventures, telling ITER's in-house magazine, Newsline: "There is no scandal here. Such things happen, I've seen many issues of the kind, and much worse."
What is ITER?
ITER is a major international project to build a tokamak fusion device in Cadarache, France, designed to prove the feasibility of fusion as a large-scale and carbon-free source of energy. The goal of ITER is to operate at 500 MW (for at least 400 seconds continuously) with 50 MW of plasma heating power input. It appears that an additional 300 MWe of electricity input may be required in operation. No electricity will be generated at ITER.
Thirty-five nations are collaborating to build ITER - the European Union is contributing almost half of the cost of its construction, while the other six members (China, India, Japan, South Korea, Russia and the USA) are contributing equally to the rest. Construction began in 2010 and the original 2018 first plasma target date was put back to 2025 by the ITER council in 2016.
Will this delay the ITER timeline?
The current timeline for ITER is for first plasma in 2025 and the start of deuterium-tritium operation in 2035. But as previously reported by World Nuclear News, that timeline was already set to be revised this year, with the defects and identification of the repair requirements set to add to existing delay pressures partially blamed on COVID-19.
Workers examine cooling pipes on the surface of the vacuum vessel thermal shield (Image: ITER)
The duration and costs of the repairs cannot yet be estimated, with Barabaschi saying: "A substantial amount of time is required and time always costs money. But we can take advantage of the present situation to reorganise and increase the experimental content of the operational phase and reach full-power operation, our real and final objective, with minimum delay."
What are the defects?
The vacuum vessel thermal shields are about 20 mm thick and contribute to insulating the superconducting magnet system operating at 4K, or minus 269°C. ITER says the issue with the thermal shield panels "is one of 'stress corrosion cracking' that is affecting the cooling pipes welded to the component surface. In the course of the manufacturing process, chlorine residues were trapped in tiny pockets near the welds, causing cracks up to 2.2 mm deep. The problem was identified on three, yet-uninstalled vacuum vessel thermal shield panels. (There are two outboard panels and one inboard panel for each of the nine vacuum vessel sectors, or 27 panels in all)". "When you find three instances of cracks, it is a red alarm because there could be hundreds of locations where cracks could develop," says Barabaschi.
The other issue relates to "dimensional non-conformities discovered in the three vacuum vessel sectors that have already been delivered". These vacuum vessel sectors are as heavy as an Airbus 380 and their height is equivalent to a five storey building. The D-shaped vacuum vessel sectors are formed from four segments welded together, so need very precise dimensions, and it was during the welding process that the "deviations from nominal dimensions occurred in different locations on the sectors' outer shells".
What's the fix for the thermal shields?
A decision was taken to remove and replace all cooling pipes, some 23 kilometres in total, from the thermal shield panels. Work is continuing to answer the question of whether the removal of the pipes "would alter the panels' dimensions, rigidity, or their capacity to accommodate a new set of piping". ITER Tokamak Assembly Specialist Brian Macklin says that solutions for the pipes and the attachment process include using a different steel formulation which is more resistant to corrosion. "For joining the pipes to the panels we contemplated using clamps rather than welds, but concluded that welding was still best, provided we use a lower-energy process and slightly different welding wire."
Checks are taking place on the impact on the thermal shield panel of removing the cooling pipes (Image: ITER)
Once the industrial partner is selected by the tender - the target date for this is the end of March - there will be discussions about where the repairs will take place - on-site or elsewhere. Some panels may also need to be re-manufactured. The working assumption is that the issue could be systemic, and could also affect the lower cryostat thermal shield which is already installed in the assembly pit. Because of the difficulty of lifting it back out, a decision has been taken to leave the original cooling network in place, disconnect it and attach a new set of pipes to replace it.
What's the fix for the vacuum vessel sectors?
To ensure that the giant vacuum vessel sectors fit together "valleys must be filled and hills must be shaved to restore the geometry to nominal and recover the ability to weld the sectors together". Macklin tells Newsline: "Machining is best, depositing metal is a bit more risky. We will need to combine both options." Some 73 kg of filler material will be required for sector #6 alone, the one which is already installed in the assembly pit, 100 kg for sector #7 and 400 kg for sector #8.
The French nuclear regulator, Autorité de Sûreté Nucléaire, is involved in the discussion of repair option. ITER says that the "deposited material will be subject to 100% non-destructive examination by either radiography or ultrasonic testing". It adds that "we are pursuing a very aggressive schedule to perform molten metal deposition tests on 'coupons' provided by the manufacturer, to carry out welding simulations at our industrial partner ENSA, and of course to select contractors in order to have everything ready to go in June".
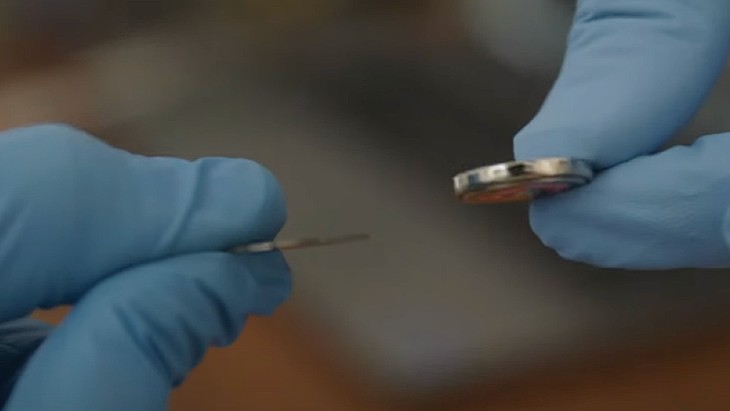
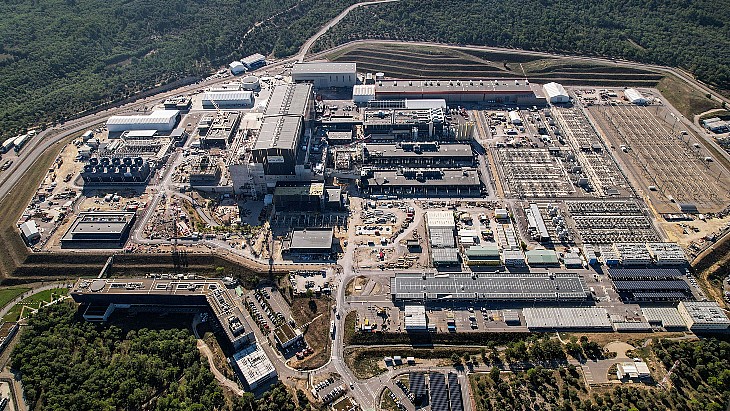
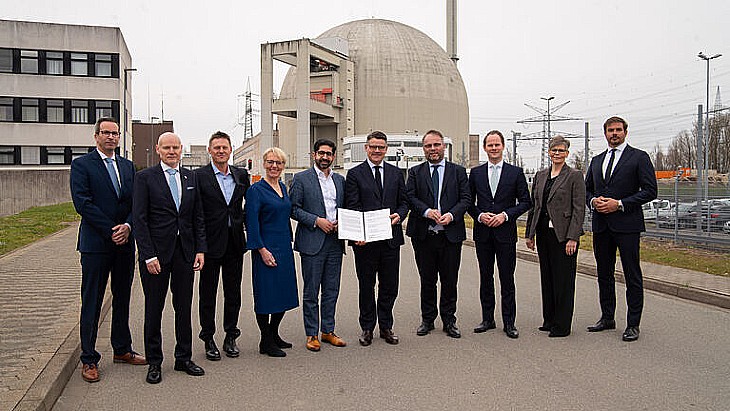
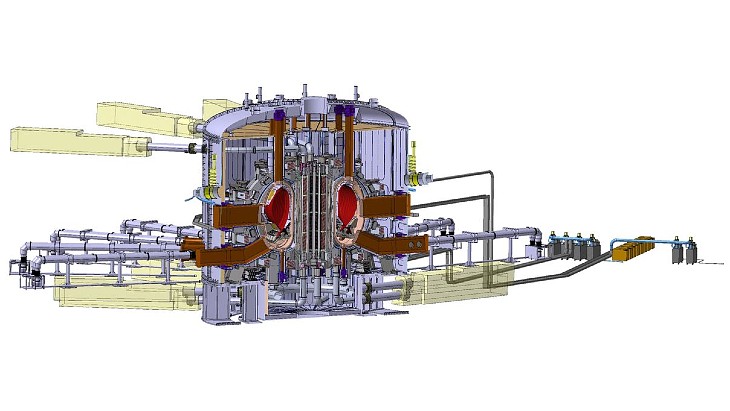
