MPC lid welding passes US regulatory inspection
.jpg)
Holtec's MPC is a single versatile package equally suitable for on-site storage, transport, and permanent disposal in a future repository. It consists of a cylindrical shell, baseplate, lid, port covers and closure ring that form the confinement boundary for the stored fuel assemblies. The confinement boundary is a seal-welded enclosure of all stainless steel construction.
Holtec noted the ongoing COVID-19 pandemic "presented new and evolving challenges" for the welding dry run, which was conducted at Holtec's technology campus in Camden, New Jersey. The Holtec and Exelon team practised social distancing and reinforced health and safety practices throughout the inspection. Using thorough pre-job briefs, the welding dry run was successfully completed without any open items to the NRC.
Following the initial welding dry run, a second dry run for drying and backfill operations for Peach Bottom only was successfully completed at the Peach Bottom plant in Pennsylvania, again without any issues identified by the NRC. A joint second dry run is planned to be held at Holtec's Camden technology centre in the coming months so that Ginna, Limerick, Nine Mile Point and Calvert Cliffs can participate and fulfill their dry run commitment for drying and backfill operations at their respective sites.
"Considering the vital confinement function rendered by the lid-to-shell closure weld, Holtec employs the largest weld size in its canisters in the industry," said Steven Soler, Holtec's director of domestic site services. "I trust the extremely conservative welding requirement imposed on our MPCs provided the assurance of added safety margin to NRC officials."
Dave Lewis, Exelon vice president of outage planning and services said the initiative to perform a single NRC demonstration of cask welding "reduces the regulatory burden" of required inspections for each used fuel campaign.
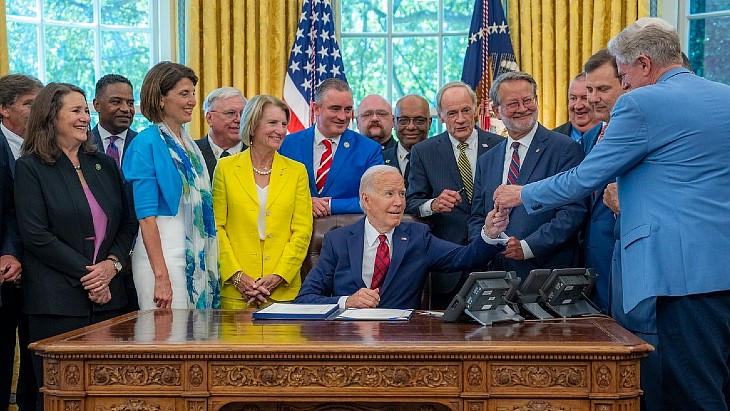
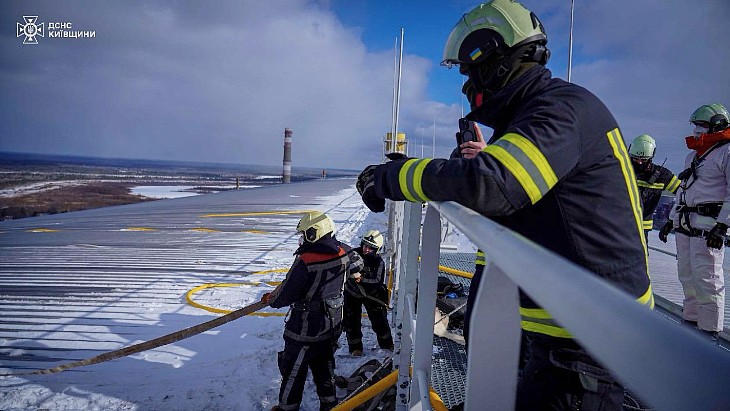
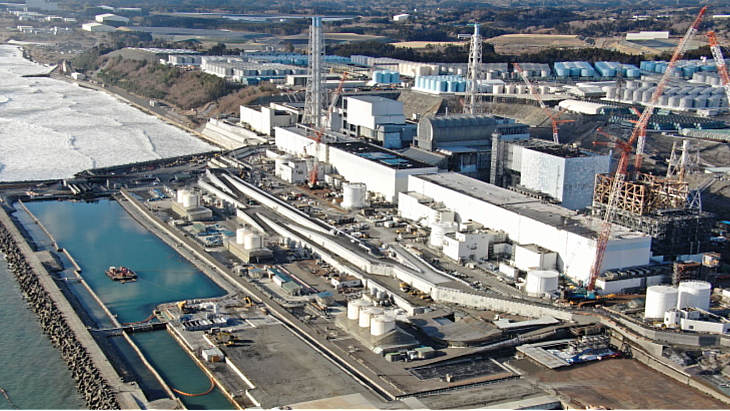
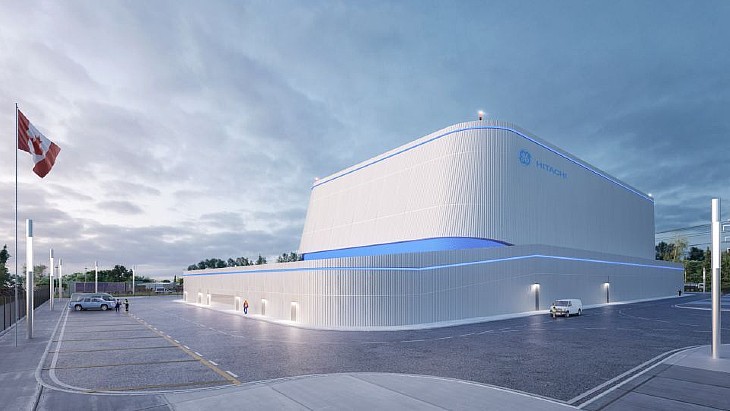
