3D innovation for Sellafield
Sellafield Ltd is pressing cutting-edge 3D printing technology into service to help meet the challenges of decommissioning one of the world's oldest and most complex nuclear sites.
![]() |
Sellafield's Donna Connor investigates the results of 3D printing (Image: Sellafield Ltd) |
3D printing is a way of manufacturing metal or plastic parts directly from design data, using lasers to fuse together high-performance materials layer by layer. The technique enables components, including one-off specialist items, to be made relatively quickly from 3D design data, which can even be obtained by scanning an existing item. Metal parts can be printed in a wide range of materials including titanium, stainless steel and brass, to a high resolution.
Sellafield's head of technical capabilities Donna Connor described 3D scanning and printing as the "holy grail" for materials scientists, offering many opportunities. Sellafield's plants, some of which were built several decades ago, are unique and include many parts which are one-off designs - the Magnox reprocessing plant was designed to operate for 20 years but is still in operation 50 years later. Up to now, Connor explained, replacement parts for such plants would have to be custom-manufactured, which is an expensive and time-consuming process. The new technology, however, offers the chance to make components relatively quickly and easily, saving both time and money.
According to Sellafield managing director Tony Price, the high definition achieved by the printing process makes parts that are more accurate, stronger and more reliable than those produced using traditional techniques. The company has already saved £25,000 ($42,000) on a single project when it used 3D blue-LED scanning technology to design a replacement lid for a 40 tonne solid waste transfer container. At about £3000 ($5000) the 3D scan cost a fraction of the price of using conventional metrology methods and the part was manufactured in substantially less than the six months it would have taken by conventional tooling.
Sellafield Ltd claims to be the first nuclear company to be pioneering the new technology, working with using 3D specialist companies 3T RPD and Central Scanning to create metal and plastic components, parts and one offs.
Researched and written
by World Nuclear News
_17992.jpg)
_75800.jpg)
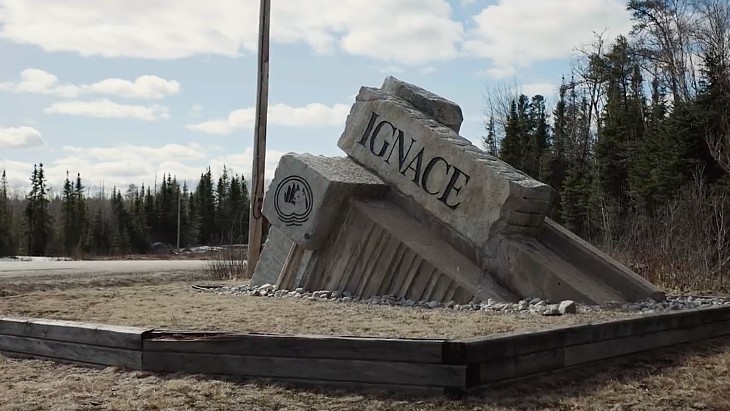
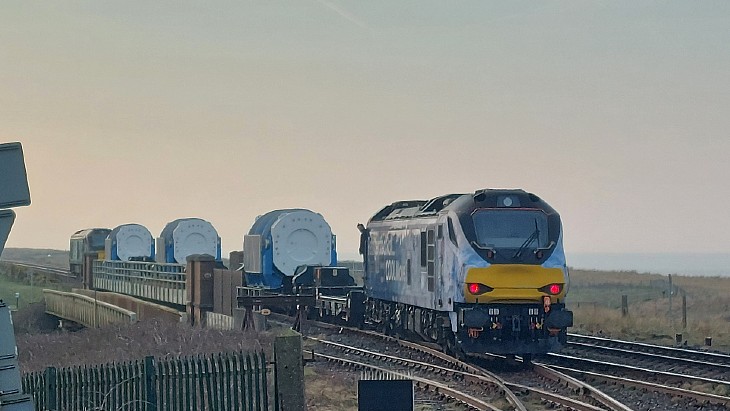
