Nukem completes mock-up of waste cementation system
.jpg)
The company said that the cementation plants it developed can treat a wide range of radioactive wastes, including high saline vaporiser concentrates, radioactive ash from incineration plants, ion exchange resins, absorber and filter materials, radioactive sludges, as well as naturally occurring radioactive material (NORM) waste and hazardous waste from oil and gas production plants, refineries and chemical or medical industry.
During barrel cementation, liquid radioactive waste is enclosed in a 200-litre barrel. The end products are externally uncontaminated steel drums containing immobilised waste in a cement matrix. The system includes: the in-barrel mixer; all necessary drum handling systems such as grippers and roller conveyors; barrel transfer and capping/uncapping systems; dosing system for liquid additives and radioactive liquid waste; a camera system; a filling station for dry material; a tracking system; radioactivity monitoring; wipe test; a weighing system for the barrels; and an overflow sensor.
The entire process is designed to operate automatically, minimising the need for operator intervention. A unique QR code is generated for each barrel, containing important information about the waste and ensuring transparency and traceability throughout the entire process.
The hot cell where mixing operations take place features a high-density inflatable pneumatic seal system that prevents leaks during liquid waste pumping and dosing operations. Nukem Technologies said the in-barrel mixer with its four degrees of freedom ensures a completely homogeneous mixture and excellent product quality in terms of compressive strength and leaching rate for radionuclides in the final cement product.
The entire system, including the in-barrel mixer, roller conveyors and other components, is controlled remotely from a central control centre. The operating personnel have real-time insight into the ongoing processes and can react quickly to deviations.
"Before being used in nuclear facilities, machines and equipment for waste treatment are thoroughly tested in full-scale test facilities, so-called mock-ups," Nukem Technologies noted.
Announcing the completion of a mock-up of its in-barrel cementation system, the company said: "This milestone represents significant progress in the safe and efficient treatment of radioactive waste generated during the operation and dismantling of nuclear power plants and nuclear facilities."
"We have installed the system here to fully test the automated operation of the system and check each and every step and individual component," said Felix Langer, technology officer at Nuken Technologies.
He added: "The training of the staff in the mock-up facility allows the operator staff to start working efficiently, to know the system already in detail when it is installed. This speeds up installation and reduces errors during operation."
_17992.jpg)
_75800.jpg)
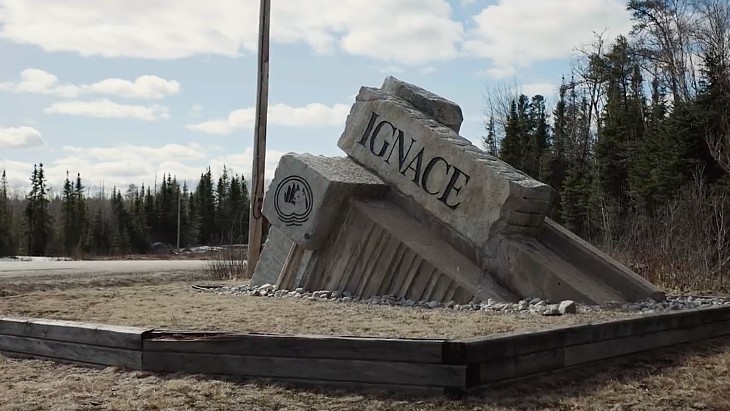
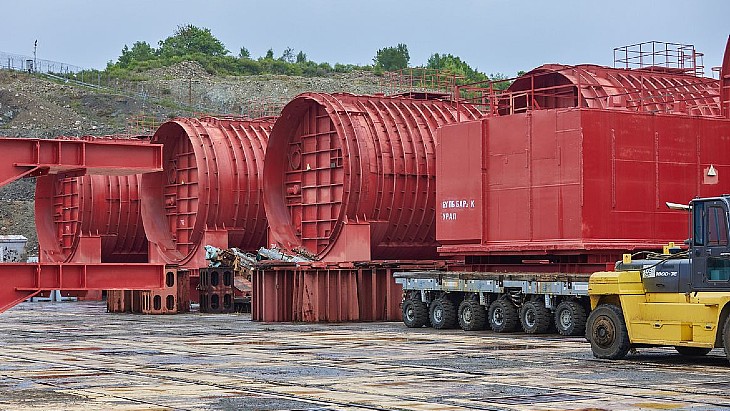
